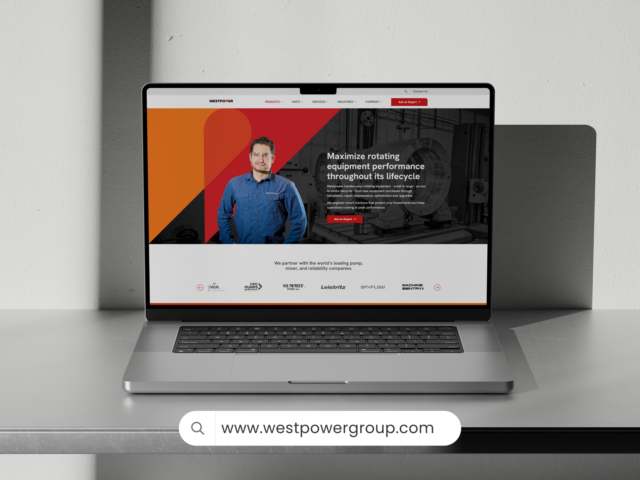
For an oil & gas operator in Alberta, maintaining Blackmer sliding vane pumps in-house became a growing challenge. Limited manpower and increasing repair demands led to inefficiencies, longer downtime, and higher costs. Westpower provided a streamlined repair and stocking program to improve efficiency, reduce turnaround times, and lower costs.
Challenge: Limited Manpower and Inefficient In-House Repairs
The client had been handling Blackmer pump repairs internally for years, but this approach was straining resources:
- Manpower Shortages: In-house repairs took technicians away from critical maintenance tasks in the field.
- Vendor Management Struggles: Coordinating multiple suppliers for spare parts created delays and administrative headaches.
- Unplanned Downtime: Without a structured repair process, pumps remained out of service longer than necessary.
With an increasing workload, it became clear that outsourcing this process to a reliable vendor would free up resources and improve operations.
Westpower’s Solution: A Dedicated Blackmer Pump Repair & Stocking Program
To resolve these challenges, Westpower developed a structured Blackmer Repair & Stocking Program to ensure fast turnaround times and optimized cost savings. Key elements included:
- Batch Repair Process: The client sends failed pumps monthly for repair, ensuring continuous equipment availability.
- Pre-Purchased Spare Parts Inventory: Westpower stocks critical components in advance, eliminating lead time delays and leveraging bulk purchase discounts.
- Efficient Repair Workflow: Pumps are rebuilt using Westpower’s dedicated repair process, run-tested, and promptly returned to minimize time off-site.
By integrating a proactive stocking program with expert pump refurbishment, Westpower eliminated logistical headaches and ensured quick turnaround times.
Outcome: Increased Efficiency, Cost Savings, and Reliability
With the Blackmer Repair & Stocking Program, the client has achieved:
- Increased Manpower Availability – Maintenance teams can now focus on high-priority site tasks instead of handling pump repairs.
- Faster Turnarounds – Pre-stocked parts and an optimized repair process significantly reduce downtime.
- Lower Overall Costs – Bulk purchasing and streamlined repairs drive down total maintenance expenses.
By outsourcing pump repairs to Westpower, the client now benefits from a reliable, cost-effective solution that ensures their operations run smoothly without disruption.