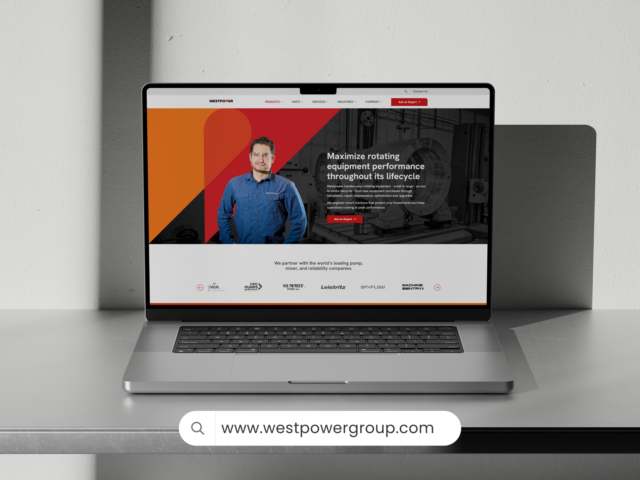
Challenge: Erosion and Wear Impacting Pump Performance
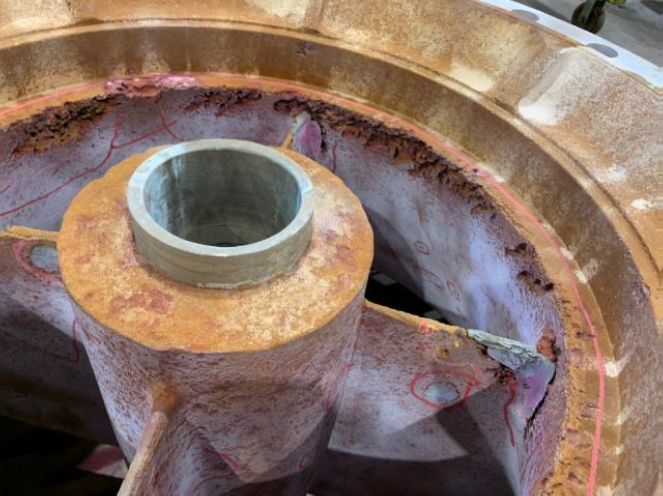
Operating in Alberta’s Wood Buffalo Region, a major oil and gas producer faced significant challenges in maintaining their large vertical river water pumps. These pumps, essential for operations, suffered from extreme erosion due to abrasive river water, particularly during the spring thaw when sediment levels were highest. Key pain points included:
- Erosive Damage: The abrasive nature of river water, particularly during springtime, causes significant damage to pump suction bells and impellers, typically requiring repairs after an average service life of six years.
- Limited Service Life: Impellers typically lasted only two repair cycles before becoming unrepairable.
- Material Limitations: Original cast iron suction bells lacked durability in this harsh environment.
Westpower’s Solution: Reverse Engineering and Engineered Repairs for Long-Term Performance
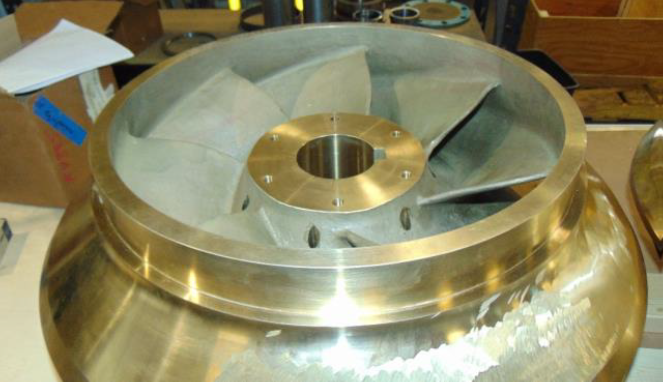
Westpower, the client’s trusted partner since the mid-2000s, provided engineered pump repairs and component replacements to extend MTBF and reduce overall maintenance costs. Key solutions included:
- 3D Scanning and Reverse Engineering: Using advanced metrology and scanning technology, Westpower precisely replicated critical components, ensuring optimal fit and function.
- Material Upgrades: Upgraded suction bells and wear components to more durable materials, enhancing resistance to erosion and improving longevity.
- Replacement Parts: Reverse-engineered impellers and suction bells supplied at reduced cost and lead time compared to the OEM, ensuring cost-effective repairs.
- Spare Parts Strategy: Collaborated with the client to maintain a stock of long-lead-time cast parts, significantly reducing repair downtime.
With Westpower’s expertise in manufactured parts, reverse engineering, and metrology, this oil and gas producer continues to benefit from increased pump availability, reduced maintenance costs, and optimized equipment performance.