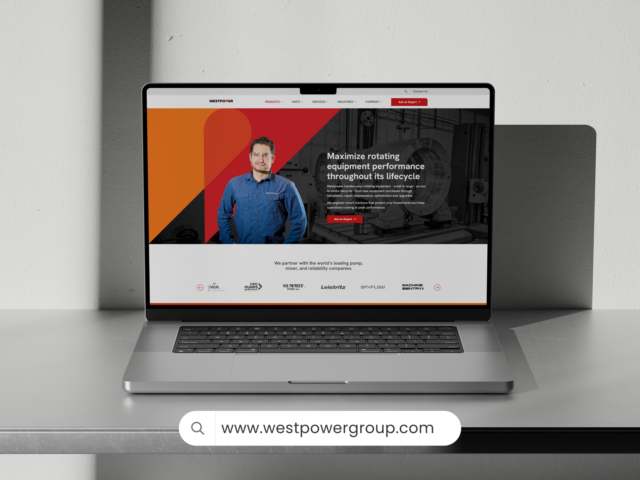
Objective: Enhancing Heavy Crude Oil Pipeline Throughput
Westpower was approached by a client to look at increasing the throughput of a high temperature, insulated pipeline that delivers undiluted heavy crude oil. The client forwarded site performance data to Westpower along with two pumps – a 3-stage pump and a 4-stage pump. At Westpower’s Edmonton repair facility, the pumps were disassembled, and the hydraulic geometry was measured and recorded utilizing laser scanning and 3D modelling. This information was used to estimate the hydraulic performance, then compared with the site operating data. The hydraulic analysis showed that the estimated performance was very close to the site data and that new impeller designs would be required to approach the ultimate conditions needed by the client.Hydraulic Design Approach: Maximizing Performance Efficiency
To achieve the maximum generated head for the pumps, several design changes were implemented. The impeller diameters were increased to the maximum allowed by API and the outlet width of the impeller was increased to match the 4-stage pump impeller width. This required volute side wall milling on all the stage-3 pumps. The pumps were removed from the pipeline one-at-a-time to keep the pipeline flowing at capacity. Additionally, Westpower supplied one 4-stage and one 3-stage spare rotors, totaling 13 pumps and 15 rotors. The old shafts from each pump were repaired or replaced as required and then fitted with new impellers for the next pumps in rotation. This process was repeated until all 13 pumps were upgraded.
Results: Increased Flow & Pressure Gains
As more pumps were changed out, the pipeline throughout increased incrementally and dramatically. All 13 pumps have been put into service and tested. The site data provided reflects the performance achievements as indicated below:
Pipeline Flow Rate Improvements:
- Initial Flow Rate: ~363 m³/h (1600 GPM)
- New Flow Rate: ~500 m³/h (2200 GPM)
Pump Performance Enhancements:
- 3-Stage Pump P209:
– Initial Differential Pressure: 2300 kPa
– New Differential Pressure: 4200 kPa (83% increase)
- 4-Stage Pump P810:
– Initial Differential Pressure: 3656 kPa
– New Differential Pressure: 5050 kPa (38% increase)
Westpower’s innovative hydraulic engineering approach was used to develop a performance curve based on the as-found hydraulic geometry for the existing impellers and casings. The new impeller designs were interchangeable across both the 3 and 4 stage pumps while keeping within the motor rating (less than 1250 HP) for the 3-stage pumps.
As a result of Westpower’s innovative and cost-effective engineering capabilities, the successful pump re-rates significantly increased performance levels and matched the new pump curves submitted by Westpower for the 3 and 4 stage upgraded pumps.
The project was very successful not only because it was delivered on time and on budget, but it was also completed with minimal disruption as the pumps were swapped out of service one at a time. The due diligence of the project team in all aspects of project management surpassed customer expectations.