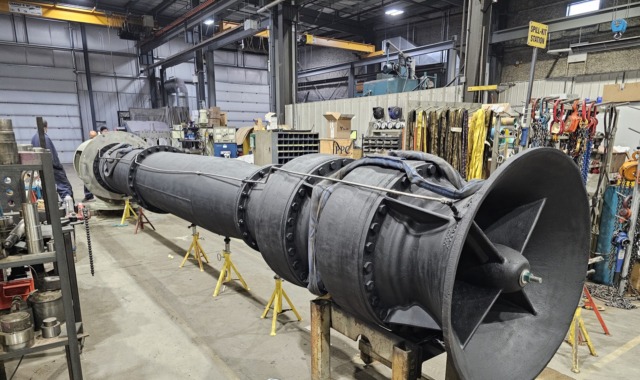
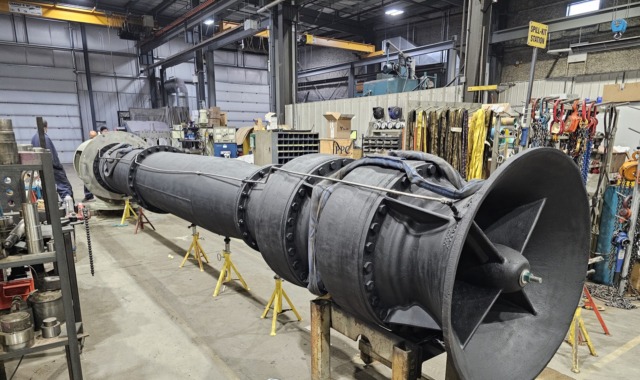
Westpower provides expert and engineered pump repair, ensuring reliability throughout your equipment’s lifecycle. We are an authorized repair center for leading pump manufacturers and provide OEM parts and specifications on those repairs. Additionally, we repair all pump makes and models, with the option to incorporate non-OEM or upgraded parts to enhance durability and performance. Our engineers and technicians deliver precision service to minimize downtime and optimize reliability, helping reduce operating costs and extend equipment life with tailored repair solutions.
Nearly 80% of a pump’s total ownership cost comes after purchase, making maintenance and repair critical to reliability and performance. Discover how Westpower’s engineered pump repair services keep your systems running efficiently.
Surface Engineering Solutions
Westpower’s in-house HVOF (High Velocity Oxygen Fuel) coating facility applies industry-standard powders and our own proprietary high-performance nano-structured coatings to protect pump components from erosion, corrosion, and wear. Our in-house ultra-high speed laser cladding capabilities further enhance our engineered surface solutions. Our engineers and metallurgists select the optimal coating formulation based on your application’s requirements and component geometry to restore critical parts, improve efficiency, and extend equipment life in harsh operating conditions. With advanced application and machining capabilities, we deliver engineered solutions tailored to your industrial and process pump repair needs.
Machining
Our precision machining capabilities ensure exact tolerances and superior fit for critical pump components. From restoring worn parts to manufacturing new high-performance components, our in-house machining supports reliable, high-quality pump repairs. Combined with our applications, design and engineered repair expertise, we deliver the accuracy and durability required for demanding process applications.
Welding
Westpower’s welding capabilities provide precision and proper welds for a full range of process pump repairs and rebuilds. Our certified welders specialize in restoring critical pump components such as casings, covers, and impellers. We ensure the performance of your rotating equipment through expert welding tailored to demanding process applications. Westpower is CWB and ABSA certified and follows strict welding procedures, with a team of highly trained and certified welders and engineers ensuring proper engineered welds for every application.
Parts Replication and Optimization
Westpower combines advanced 3D scanning, expert craftsmanship, and engineering resources to provide reconstructive engineering and manufacture high-quality pump components. Our team transforms raw data into precise drawings, then fabricates components that meet or exceed original specifications. We optimize designs to improve reliability and extend Mean Time Between Repairs (MTBR), reducing maintenance costs and maximizing uptime.
Specialized Engineering
Our internal engineering services focus on optimizing industrial and engineered pump repairs through expertise in applications, hydraulics, metallurgy, and mechanical design. Tailored engineering solutions improve pump performance, efficiency, and reliability in demanding environments. Each repair is designed to meet the specific needs of your system for long-term operational success.
Material Assessments and Upgrading
Our material assessments and upgrades ensure your process pumps are built or upgraded to withstand their unique operating conditions. Our engineers evaluate material performance and recommend upgrades to enhance reliability and reduce erosion/corrosion. With tailored solutions, we keep your pump performing at its best.
Material Stocking Programs
Our material stocking programs ensure you have quick access to critical pump components and raw materials when you need them most. We work with you to maintain an inventory of high-demand parts, reducing downtime and streamlining repairs. Work with us to minimize delays and maintain operational efficiency.
OEM Pump Part Inventory
We maintain an extensive inventory of OEM pump parts to ensure fast, reliable repairs for your process pumps. By sourcing and stocking genuine OEM components, we reduce lead times and ensure your equipment runs with the best parts available. As your OEM representative, we also facilitate parts sourcing and provide expert support.
Non-Destructive Testing & Analysis
Each of our facilities has in-house capabilities and also partners with experts in non-destructive testing techniques, such as MPI (Mag Particle Inspection), LPI (Liquid Penetrant Inspection), RT (Radiography testing), and UT (ultrasonic testing). Our engineers use NDE test results to develop strategies for repairing and replacing components. Each of our facilities has hydro testing capabilities to ensure casting integrity, and Westpower Group operates a full performance test stand to ensure pump performance as required.
Component and Rotor Balancing
Each repair facility is equipped with multi-plane balancing for all necessary components and assemblies. We balance to better than API 610 as a standard or other specifications per client instructions.
Pump Re-Rates and Upgrading
Our pump re-rating and upgrading services optimize your equipment for changing process demands or to increase MTBR. Based on your goals, our engineers offer hydraulic, mechanical, and metallurgical/material modifications to improve your pump performance.
Off-site / In-House Pump Repair
Westpower offers both repairs in the field by qualified technicians and at our multiple repair facilities. Our field technicians provide on-location troubleshooting, disassembly and reassembly, while complex repairs are handled at our repair facilities. Westpower’s expert repairs optimize pump performance and reduce operational disruption.
Westpower’s advanced pump repair centers in Calgary and Edmonton are equipped with boring mills, lathes, grinders, dynamic balancing machines, and HVOF coating systems for complex pump repairs. Our specialized team of qualified tradespeople includes machinists, millwrights, and welders who work with our engineers to restore API, ANSI, ASME, and other industrial pumps. Our in-house expertise in machining, boring, balancing, and coating ensures high-quality and timely pump repairs and upgrades for all of your sites across Western Canada.
We’ve yet to receive a pump that we couldn’t repair, overhaul, and return to service. We specialize in a wide range of pump repairs, including centrifugal, reciprocating, vacuum, axial piston, diaphragm, and screw pumps, from fractional HP metering pumps to over 5000 HP process, power generation, and pipeline pumps. Our expertise covers ISO, API, ASME/ANSI, Hydraulic Institute and other industrial standards across various pump categories for all types of positive displacement and centrifugal pumps.
Westpower provides complex pump repairs for all OEM brands we represent, as well as most others across the industry. With a brand-agnostic approach, we provide tailored solutions for rotating equipment backed by expertise in Western Canadian requirements. Our team ensures reliable, high-performance repairs to keep your equipment operating optimally.
Westpower delivers specialized repair solutions for centrifugal and positive displacement pumps, mixers, and other rotating equipment, covering everything from field part replacements to advanced rebuilds. Whether addressing basic repairs, balancing, or complex engineering work, our experienced team ensures precision and reliability. We handle every repair with care, boosting performance and minimizing downtime for your equipment.
Repair Complexity | Standard IndustrialWestpower’s industrial repair team handles routine maintenance, including disassembly, inspection, seal and bearing replacement, wear ring replacement, and impeller balancing to keep your pump running efficiently. | IntermediateWe go beyond the basics with rotating assembly balancing, minor casting repairs, and shaft alignment, ensuring optimal performance and extended equipment life. | Complex EngineeredOur engineers tackle hydraulic rebuilds, major casting repairs, shaft replacements, hydrotesting, and custom upgrades, delivering solutions for the most demanding applications. |
Pump Disassembly and Inspection | X | X | X |
Seal Replacement | X | X | X |
Bearing Replacement | X | X | X |
Wear Ring Replacement | X | X | X |
Impeller & Component Balancing | X | X | X |
Rotating Assembly Balancing | X | X | |
Casting Repairs (Minor) | X | X | |
Shaft Alignment Check | X | X | |
Hydraulic Component Repair (Impeller, Diffuser, etc.) | X | ||
Shaft Repair/Replacement | X | ||
Casting Repairs (Major) | X | ||
Custom Upgrades (Materials, Performance, etc.) | X | ||
Hydrotesting of Pump Components | X | ||
Full Documentation and Certification | X | ||
Emergency & Urgent Repairs | X | ||
Hazardous Applications (NORMs, H2S, etc.) | X |
Repair Complexity | Standard IndustrialWestpower’s industrial repair team handles routine maintenance, including disassembly, inspection, seal and bearing replacement, wear ring replacement, and impeller balancing to keep your pump running efficiently. | IntermediateWe go beyond the basics with rotating assembly balancing, minor casting repairs, and shaft alignment, ensuring optimal performance and extended equipment life. | Complex EngineeredOur engineers tackle hydraulic rebuilds, major casting repairs, shaft replacements, hydrotesting, and custom upgrades, delivering solutions for the most demanding applications. |
Pump Disassembly and Inspection | X | X | X |
Seal Replacement | X | X | X |
Bearing Replacement | X | X | X |
Valve & Seat Replacement | X | X | X |
Plunger & Packing Replacement | X | X | X |
Gasket & Fastener Replacement | X | X | X |
Power End Overhaul | X | X | |
Fluid End Rebuild | X | X | |
Crosshead & Bearing Replacement | X | X | |
Custom Performance Enhancements | X | ||
Hydrotesting of pump components | X | ||
Full Documentation and Certification | X | ||
Performance Testing (Upon Request) | X | X | X |
Screw/Rotor repair or replacement | X | ||
Stator/Liner repair or replacement | X | ||
Plunger/Diaphragm inspection and replacement | X | ||
Timing Gears/Power Transmission overhaul/inspection | X |
Pump systems evolve, and so do their operational demands. Westpower’s 4R approach: Redesign, Rerate, Remanufacture, Replace, ensures your pumps perform optimally in any condition. Whether upgrading, adapting, or replacing, our engineered solutions deliver efficiency, reliability, and cost savings.
We enhance OEM designs to improve Mean Time Between Repairs (MTBR) and resolve operational challenges. By strengthening weak points in the original design, we address system changes and evolving application demands. Our redesigns include material upgrades, rotor modifications, optimized hydraulic passageways, and bearing housing enhancements.
We modify pump hydraulics to better match current or future desired operating conditions, optimizing efficiency and performance. This process typically involves hydraulic modifications with our in-house engineering to design and manufacture components.
We refurbish surplus new or used equipment to meet specific operational requirements, reducing lead times and ensuring seamless integration. Remanufacturing allows for much quicker lead times than manufacturing a new pump while meeting all of your operational requirements.
We provide exact pump replacements to eliminate costly site rework, avoiding modifications to piping, baseplates, or electrical infrastructure. Where beneficial, we can also integrate redesign and rerate enhancements within the existing pump envelope. This is most often requested when the OEM will no longer support an older pump design, the OEM cost and delivery is excessive, or facility retrofits such as piping are prohibitively expensive.
We don’t just fix pumps, we improve reliability and reduce lifecycle costs with smarter solutions.